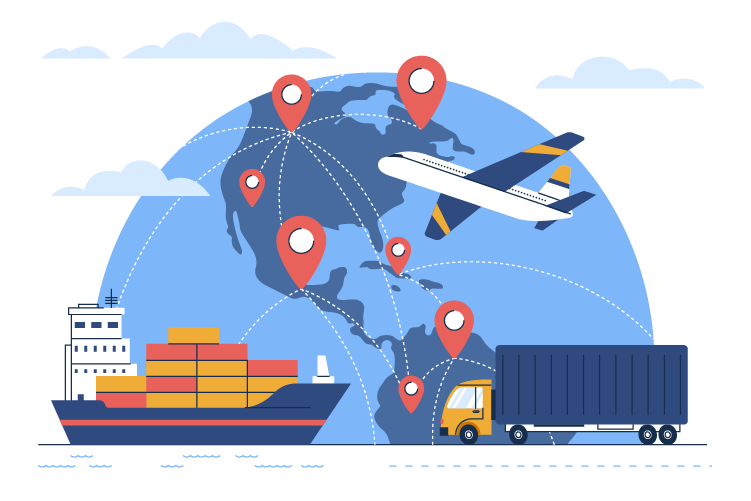
When They Need Help With Inventory, Warehousing, And Logistics Optimization?
Have significant excess and obsolescence issues? Not able to hit warehouse KPIs? Don’t have the right KPIs for the warehouse? Kano Andalan’s inventory, warehousing, and logistics optimization services are designed to help companies when they struggle with these challenges.
Excess And Obsolescence Issues With Inventory
Struggling to plan excess inventory? Have inventory in the warehouse that’s aging and not turning as frequently? Companies seek help from Kano Andalan when they run into issues with excess and obsolete inventory.
Not Able To Hit Warehouse KPIs
Struggling to hit warehouse KPIs because the warehouse is disconnected from the ERP? Running into significant allocation issues? Companies seek help from Kano Andalan when they are not able to hit their warehouse KPIs.
Don’t Have The Right KPIs For The Warehouse
Do you not measure the total time taken with the dock-to-stock process? Picking and packing processes are tightly coupled, and no clear process for decoupling picking and packing process. Companies seek help from Kano Andalan when they might not have the right KPIs for the warehouse.
Operational Transactions Resulting In Significant Variances
Do your warehouse transactions result in significant variances that your accounting teams take forever to resolve? Always struggling to reconcile the inventory after your cycle counting process? Companies seek help from Kano Andalan when operational transactions might result in significant variances.
Logistics Planning Not Working
Significant issues with logistics planning? Packages always arriving damaged? Scheduling and dispatch always a challenge? Companies seek help from Kano Andalan when they need help with logistics planning.
Challenges In The Dispatch To Receive Process
Significant issues in the proof of delivery process? Matching issues in the dispatch to receive process? Companies seek help from Kano Andalan when they struggle with the dispatch-to-receive process.
OUR METHOD
Our Methodology For Inventory, Warehousing, And Logistics Optimization
The process starts with an assessment to identify the KPIs and processes that might be causing inventory, warehousing, or logistics planning issues. Once identified, a thorough root cause analysis is performed. And then, as-is and to-be process models are built, including aligning all the stakeholders about the impact on their areas. And the changes that need to be made with processes, data, and systems to recalibrate planning.
Step 1: Assessment
This phase starts with identifying the KPIs and processes that might be causing planning issues. This phase also proposes several options and their pros and cons, along with the business case. An option that is least financially and technically risky is chosen for the next step.
Step 2: Root Cause Analysis
This step is a deeper dive into the chosen options and tracing processes and data that might be impacting KPIs. Through the interviews with different stakeholders, appropriate as-is and to-be process models are identified that are agreed upon by all the stakeholders.
Step 3: Implementation
This step implements the changes identified, whether they are going to be system, process, or data related. This phase could be divided into multiple phases and milestones depending upon the complexity of each change, including the identification of KPIs and how the changes would be measured after each step.
Step 4: Adoption And Optimization
Post implementation, this step helps in gathering feedback from the users if the initiative is aligned with their expectations, as well as whether the new inventory, warehouse, and optimization techniques have helped them hit their KPIs. This phase iterates until the stakeholders confirm the results of the new changes.